Personally, I have repeatedly encountered the problem when a bolt or stud breaks at the root. Moreover, I am not some kind of auto mechanic or mechanic. I say all this to mean that this quite happens to an ordinary person who periodically deals with technology or other technical parts.
Well, since you find yourself in such a situation, then don’t despair - everything can be fixed. I offer you seven ways to get out of this situation and free the thread from a broken pin or bolt.
Preparation before turning out the fragment
But don’t rush to start unscrewing right away. Before doing this, you need to take steps that will make your efforts easier.
First of all, spray the broken area with penetrating lubricant. This can be any “liquid key”, WD-40. Let's wait a little.
Next, in order to slightly relieve internal stress, we use a gas burner to thoroughly warm up the fragment and the area around it.
Well, then let’s move directly to unscrewing the broken pin or bolt.
Method 1: Flat head screwdriver and hammer
This is the easiest way, but it is not always suitable. In about half the cases, the pin breaks off with a fragment sticking out, which is just where you can get caught.
We take a flat-head screwdriver, press it against the fragment and, using impact movements at an angle in the direction of unscrewing the thread, carefully turn the fragment.

This method is suitable if it does not require much effort to unscrew. If the effort is not enough, then move on to the second method.
Method two: try to unscrew it with a chisel
This method is similar to the first one, but instead of a screwdriver we take a chisel. In the same way, we rest against the splinter and use percussive movements to turn it out.
A chisel makes it possible to create more force compared to a screwdriver.
Third method: core and hammer
If the bolt fragment does not have splinters, or even the breakage occurred just below the final surface of the thread, then you can try using a core.
We rest the core against the surface of the fragment with an offset and, with blows at an angle, we turn it out until the fragment can be hooked with pliers or another tool.
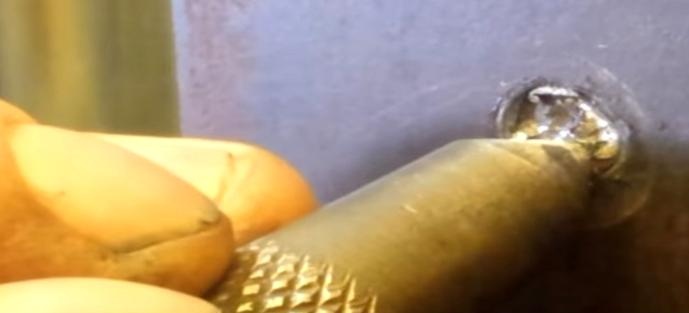
Fourth method: weld the nut by welding
In my opinion, this is the most effective and fastest option, but only if you have a welding machine. Its essence is to weld a nut onto a piece of bolt on top.
So, to do this, take a nut, but not the same size, but a couple of units larger. That is, if the broken bolt was 10, then take a nut 12. This is necessary for a better and larger welding site.
Holding the nut with pliers, we place it on the fragment, but not in the center, but offset. Using an electrode, we weld the stud and nut to one side inside the nut.
Then, after cooling, unscrew it with a regular wrench.
Fifth method: unscrew the pin with an extractor
Here you will also need a specialized tool specifically designed for unscrewing broken studs and bolts - an extractor.
We center the pin so that the drill does not run around when starting to drill.

Drill a hole of the appropriate diameter for the extractor.
We insert the extractor into the hole and unscrew it with a key.
Sixth method: drill out the fragment
The method is to select a drill according to the lower diameter of the stud thread and drill it out. A very difficult method that requires skill.
First we go through a drill of a smaller diameter.
Then we drill as close as possible.
We knock out the fragments and remnants of the stud with a flat screwdriver.
This method of removal is not always worth the effort, but it deserves your attention.
Seventh method: drill a clean hole and make an insert
The most time-consuming and expensive method of all. But there are times when this is the only working option to return the node to working condition.
We drill out the stud cleanly along with the thread.
We cut a new thread with a tap.
You can finish here if the design now allows you to select a thicker bolt or stud. If not, we buy an insert or order it from a familiar locksmith.
Lubricate the external thread with thread locker and screw it in.
Stitch flush.
What method did you use? Write in the comments, I think your experience will be interesting! All the best!
The node has been restored.