Most often, reinforced concrete floor slabs act as such a base, over which layers of coating are built:
• Reinforced concrete floor – cement leveling screed – waterproofing – subfloor made of plywood – facing wooden covering.
• Reinforced concrete floor – cement leveling screed – waterproofing – joists – vapor-proof film layer – front wooden covering.
• Reinforced concrete floor – cement leveling screed – waterproofing – joists – vapor barrier layer – plywood subfloor – facing wooden covering.
However, builders or repairmen do not always have an ideal foundation at their disposal.We are talking about houses in which the floors are not solid, but are made of metal structures, reinforced concrete or wooden beams. Buildings with extremely uneven concrete foundations and collapsed cement screeds can also be considered problematic from the point of view of repairs. Modern methods of correction, restoration and repair of the foundation using new materials - special dry compounds, lightweight concrete, leveling mixtures - allow these problems to be effectively solved, while reducing the cost construction and reducing its terms.
Ultimately, you can remove the old cement or concrete screed and create a new one. But this approach has one serious drawback that does not correspond to the modern rhythm of life - a high initial moisture content in concrete and a long, up to 3 months, pause in interior finishing work associated with the screed drying to an acceptable moisture content level. They learned to overcome this obstacle by using dry bulk screeds based on expanded clay, which have a number of advantages that traditional cement-based screeds do not have:
• Dry screeds are much lighter than cement screeds; their weight is not critical for wooden floors in old buildings.
• Screeds based on expanded clay are impeccable from an environmental point of view.
• Dry screeds are strong and do not shrink, like cement screeds.
• Due to the porous structure of the material, expanded clay screed does not remove heat from the outer layer of the floor and perfectly absorbs sound.
• It is easy to “hide” communications – pipes and cables – in the thickness of expanded clay.
• The flooring process becomes almost continuous until the work is completed.
For the installation of dry screeds, expanded clay is usually used, the porous and therefore light granules of which are obtained from baked clay.Expanded clay differs in the size and shape of granules. For dry screeds of small thickness, expanded clay sand with particles measuring 1-6 mm in diameter is used. The different diameters of the granules ensure their dense packing with small air gaps. This type of screed does not shrink over time.
Let's look at the stages of laying a floor with a dry screed device in more detail:
1. The creaking of old floors indicates wear and tear on the underlying layers of coating. To get to them, the top face layer is removed, then the subfloor and the waterproof layer underneath. Next, the logs and vapor barrier layer are removed. The old screed is destroyed using a powerful hammer drill operating in impact mode with a special nozzle.
2. Temporarily dismantle the wooden slats or metal profile that served to level the old cement-based screed. Construction debris is carefully removed until a clean surface of the floor slab is obtained.

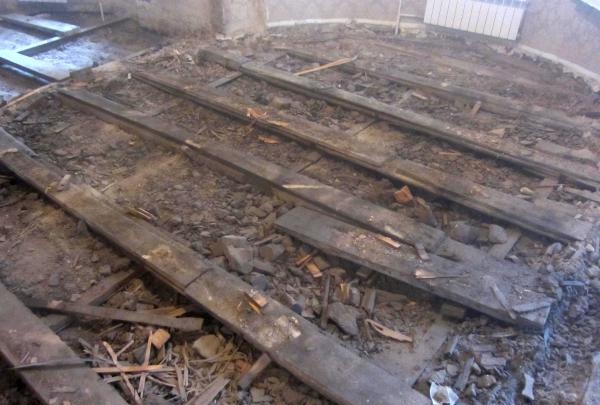
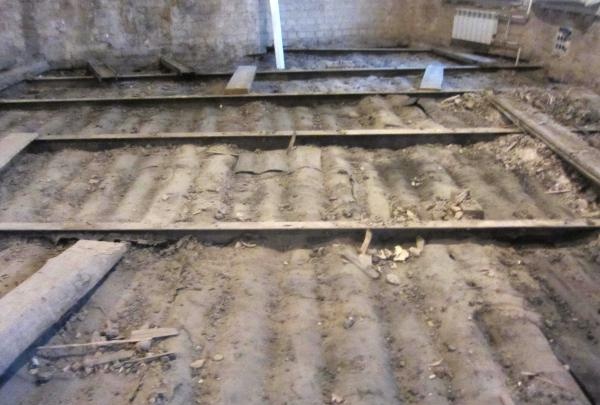

3. When moisture gets on a screed made of expanded clay sand, its properties will change - the granules will begin to stick together, and the screed will shrink. As a result, the elements of the floor elements located above will begin to shift relative to each other under load - the floors will begin to creak. To prevent contact of the dry screed material with moisture rising from below in the form of water vapor, a vapor barrier layer is placed underneath it. It can be made of thick polyethylene film, glassine, and special vapor and moisture insulating materials. Strips of film with a five-centimeter overlap are spread over the entire area of the room, bending at the walls.




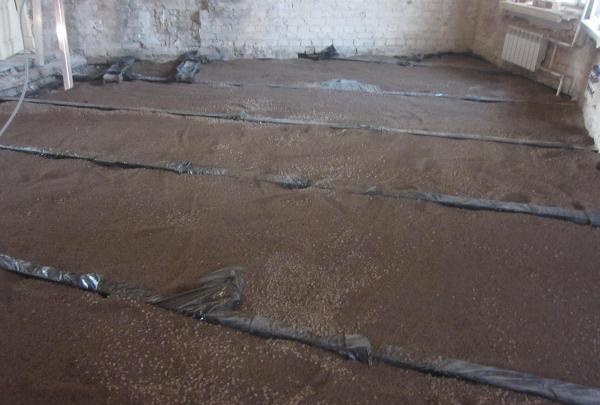
4.Along the perimeter of the room, using double-sided masking tape, an edge tape made of foamed polyethylene is attached, which serves to fix the thermal expansion joint and absorb impact noise (the sounds of footsteps will be hidden and not transmitted to neighboring rooms).
5. The top edge of the bulk dry screed should be absolutely flat in all directions. Therefore, it is first necessary to set and fix level guides in the form of metal profile strips over the entire area of the room, which will also perform some reinforcing function in the screed. This is the most complex and important operation when installing a dry screed, which determines the final quality of the entire work. When performing this, use a flat rail with a spirit level attached to it. A laser building level can also be very useful.
6. You can backfill the screed material, distributing it evenly, aligning its level along the guides. As the screed is leveled, it is useful to slightly compact it, pressing down from above, for example, with a piece of board. To obtain a high-quality screed, the amount of expanded clay sand must be such that a layer of at least 2 cm in height is obtained. Accordingly, the previously set guides must also satisfy the required geometric parameters. If necessary, move along the screed, so as not to spoil the work - after all, your feet will sink into the soft and pliable material - you need to move along the ladders of plywood or gypsum fiber sheets.
The following stages of installing a floor on a dry screed differ significantly from the technology with a cement-based screed.Traditional steps include installing joists on top of the screed to create a ventilated gap, laying insulating and sound-absorbing material between the joists, or raising the floor level. Waterproofing is spread over the joists to prevent moisture from penetrating the insulation from above. All this is covered with a subfloor, on which the facing material is laid.








In addition, there is a technology where brick columns are built on a bulk foundation, on which logs are laid through a layer of waterproofing. However, in this case we are talking about a hard cushion of crushed stone compacted into the ground. A relatively soft dry screed cannot serve as a base for brick columns. The feasibility of adding a joist over a dry screed also seems dubious. The porosity of expanded clay granules allows air movement, and the material itself provides sufficient sound absorption and thermal insulation.
7. Modern construction technologies provide for laying waterproofing and subfloor directly on the screed and its guides. Moreover, for example, a layer of moisture-resistant gypsum fiber sheets can play both roles. When laying, the sheets are tapped on top with a rubber hammer, secured to the guides with self-tapping screws and the joints are glued. Sometimes, to be sure, GVLV is laid in two layers, shifting the joints. When using plywood as a material for the subfloor, you will have to lay another layer of film underneath for waterproofing.





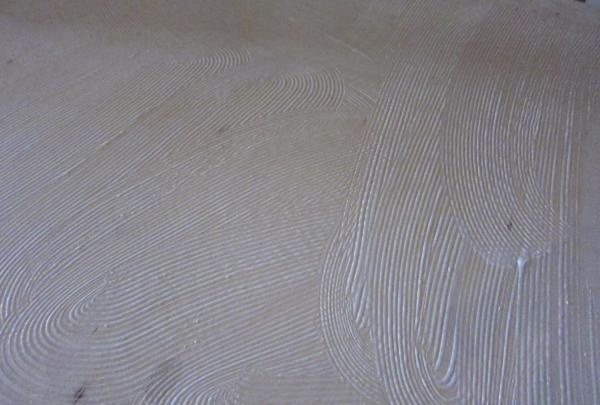
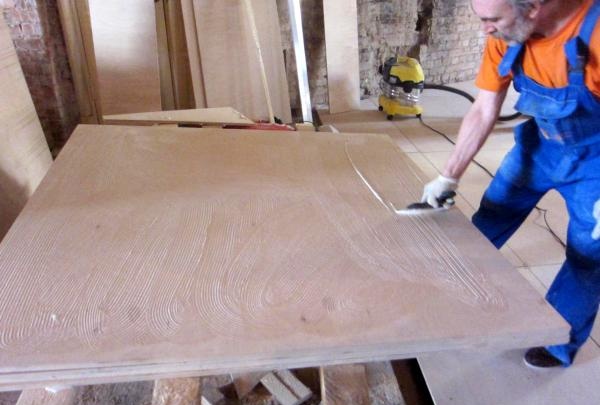



8. Excess edging tape near the walls is cut off. The subfloor is ready. Now you can lay any covering.





