But the experience of folk craftsmen shows that, even without knowledge of turning, it is possible to make a mechanical cleaver from scrap materials, adapting it to the place, amount of work and anthropometric data.
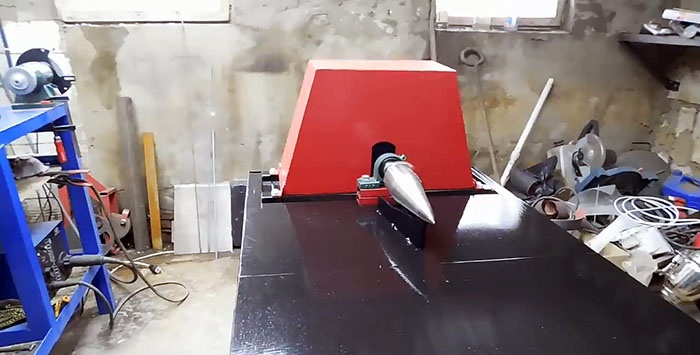
Will need
In principle, almost all materials and components for assembling a mechanical cleaver can be removed from old cars, household appliances and found in landfills. But it doesn’t hurt to know how much this or that “thing” costs in the store, how much the motor from an old washing machine will cost, what the turner will charge for the work, etc.
So, what should we stock up on if we decide to make a mechanical cleaver:
- round rolled steel (round timber);
- masking tape;
- sheet metal of different thicknesses;
- profile pipe about 14 m;
- flywheel from GAZ-53;
- bolts, nuts, washers;
- motor with pulley and belt;
- paint and brush;
- conical screw carrot cleaver.
Of the tools and equipment we should have on hand:
- grinder with discs;
- plasma cutter;
- metal file;
- welding equipment;
- vices and clamps;
- drill with drills.
Manufacturing of components and parts of the wood splitter
We secure the round timber in a vice and mark the cut locations with masking tape to quickly and easily ensure the required accuracy.

According to the markings, we cut out the wood splitter shaft blank using a grinder and a 180 mm cutting disc.
We mark the surface of a thick sheet of metal with two different-sized disks, but with identical central holes.

It is more convenient and accurate to cut them with a plasma cutter; as a result, the amount of subsequent processing is minimized.
We bring the discs to the required size with a file and a grinder, and in order not to remove excess metal, we glue precise patterns from tape or paper onto the side surfaces.

When processing disks, we pay the main attention to the central holes: the shaft workpiece should fit freely into them, but the gaps should be minimal.
This operation is one of the most important: we weld a large disk exactly at 90 degrees to the round timber. Therefore, we carry out welding carefully, constantly checking the angle between the parts so that they do not move, and we use magnetic squares. We clean the welds.
The second ring is easier to install. It is enough to press it tightly and fix it to the first disk with clamps and weld it in this position.


Now the turner will work on the workpiece: he will turn the front support, which is welded to the smaller ring, grind the circular surfaces to size and make a series of ring grooves for the drive belt.
From a profile pipe we cut blanks of the required sizes and in the required quantity, from which we weld not just a desktop, but a base for installing mounted units as well.


Separately, we weld a subframe to the main frame under the tabletop, to which the electric motor will be attached and adjusted.

Using a grinder, we cut out two symmetrical parts from a metal plate 6 mm thick, which, welded together and fixed to the tabletop, will become a kind of blade-support on the wood splitter.

Since the load on our device will constantly change, we cannot do without a flywheel. In our case, in terms of size and weight, the most suitable flywheel was from a GAZ-53 with an outer diameter of 372 mm, a mounting hole of 40 mm and a weight of almost 16 kg.

We remove the gear ring from this part and clean it from many years of oily dirt using a hammer, a screwdriver and a grinder with attachments.
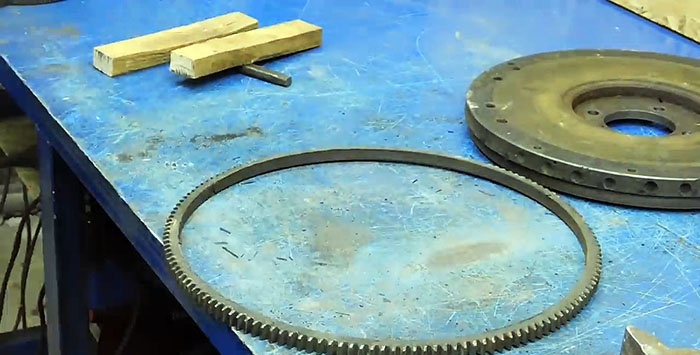
We perform static balancing of the shaft and flywheel by screwing them to each other with bolts and nuts. Due to the lack of a balancing machine, we come up with one using only available capabilities.


To do this, temporarily place two corners parallel to the table frame and lightly grab them. Using a level, we ensure that the corners are as flat as possible and place the shaft with the flywheel on them.

We give rotation to the flywheel and monitor the moment of stopping. If there is an unbalanced mass on it, it will roll back a little before stopping. Moreover, the excess mass will be at the lowest point.We mark this place and drill a hole, thereby removing excess mass.

Balancing will be considered complete when the shaft and flywheel do not roll back before stopping.
For safety, we make a protective cover for the flywheel from the remains of the profile pipe and sheet metal and cook the table top.


We connect two symmetrical parts together at an angle, place a spacer inside and weld the resulting assembly to the tabletop.

All components and parts have been made, so we begin to paint them using an ordinary brush.
Approximate costs
Let's estimate how much a homemade wood splitter will cost us:
- flywheel – 1200 rub.;
- profile pipe 14 m – 1200 rub.;
- washing machine motor (730 W, 8 thousand rpm) – 530 rubles;
- “carrot” (base diameter – 70 mm, height – 250 mm) – 1300 rubles;
- two 206 bearings in a housing – 600 rubles;
- turner work - 1650 rubles;
- hardware and drive belt – 530 rub.
The total is about 7 thousand rubles. This is 3 times less than the cheapest factory wood splitter.

Assembling components and parts of the wood splitter
We firmly screw the flywheel to the shaft, put on the belt, bearing units and secure the unit to the frame.
We install and secure the “carrot” at the end of the shaft with two special pins.


We tighten the belt by tightening the bolt intended for this purpose, which, resting against the support, moves the engine and tensions the belt.


Electrics consist of a power cord, a switch and a voltage regulator from the grinder. The connection system is quite standard.


When starting, the presence of a regulator eliminates jerking and ensures a smooth increase in speed by the flywheel. This is very important because the belt does not slip in the grooves, which means it will last longer.
Also, thanks to the voltage regulator, you can change the power, which without load immediately leads to an increase in speed.
We install a protective cover on the flywheel to protect ourselves and nearby people from injury if the flywheel suddenly flies off the shaft or cracks.
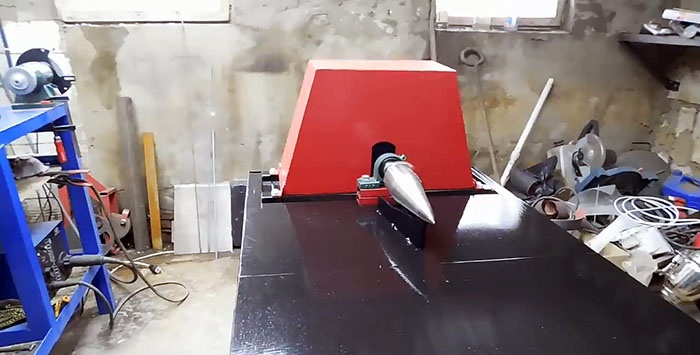
Testing a wood splitter in action
First, let's try to split a small piece of board. Our homemade product copes with it effortlessly. The same thing happens with dry logs that were stored under a canopy. The wood splitter deals with a fairly massive stump without any stress.

If suddenly the “carrot” gets stuck in a log, then by turning off the power, using the key and rotating the rear part of the shaft, we can easily free the working element from the log in which it is stuck.
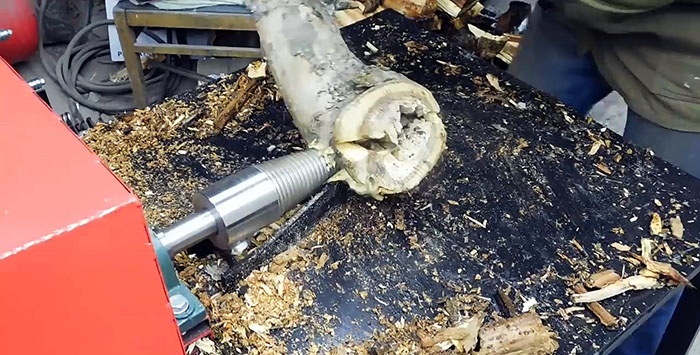
Even this small practice showed that the “carrot” fastening on the shaft should be recessed so as not to create interference when chopping firewood, and the table should stand on an absolutely horizontal surface. This will eliminate even minor vibrations during the operation of the wood splitter.
Also, you cannot work on this unit wearing gloves and mittens, and the sleeves of clothing should not be too long and without laces, belts and other hanging elements, so that they do not get twisted into a “carrot” and damage your hands.
